In this article we will present the sharpening parameters, some safety measures during sharpening and how we can increase the durability of the blade and reduce the frequency of sharpening.
The tooth profile is chosen according to the application:
for soft wood, the PV type profile is recommended, which ensures a good chip compaction;
- for hardwood we propose the PCP type profile, which ensures a good removal of sawdust;
- for slatted canvases, we advise you to use the NU and NV profiles.
The main characteristics of the tooth profile are:
- angle of attack;
- tooth height;
- tooth pitch;
- the angle of the back of the tooth;
- tooth gap radius.
From our point of view, the most important parameters and what should the client take into account when sharpening the blades is the angle of attack, which is chosen 4-5 degrees higher for soft essence than for hard essence and can have values between 10-35 degrees depending on the width of the bandsaw blades.
In practice, an incorrect angle of attack can be observed by moving the blade on the flywheel during cutting. How exactly? If the angle is too small, then the bandsaw tends to enter the flywheel and if the angle is too large, then the bandsaw tends to come off the flywheel.
The height of the tooth is the most important parameter that influences the quality of the cut as well as the durability of the blade. This parameter determines the size of the tooth gap, which in turn has a great influence on the removal of sawdust
Thus, a tooth gap that is too small does not allow the correct removal of sawdust, due to the large amount of sawdust that appears during cutting. This is best seen by placing the sawdust on the cut wood. A higher tooth height and a tooth gap that is too large helps to remove the sawdust correctly, on the other hand, it increases the risk of bending or breaking the tooth during cutting, especially in winter when the wood is frozen.
The pitch of the tooth is chosen depending on the species of wood being cut, the size of the logs or the cutting height, the speed of the blade and the amount of advance/the desired cutting speed.
Knowing these parameters we can accurately determine the optimal pitch of the bandsaw blades.
The speed of the stone for sharpening bodies with ceramic binder must be around 32 m/s and for discs with Borazon approximately 40 m/s.
For better sharpening quality and high productivity, different sharpening speeds can be chosen. Thus, on the chest and in the cavity of the tooth, a lower speed is preferable to obtain the smoothest possible surface, and on the back of the tooth, higher speeds can be used.
A fine sharpening in the hollow of the tooth greatly reduces the risk of cracks.
These adjustments can be made especially with high-performance sharpening machines, respectively those with CNC numerical control.
Details here.
At Metamob, sharpening is done on automatic CNC sharpening machines and is done on the entire surface of the teeth profile, the kinematics of the movements during sharpening contributing to obtaining a uniform teeth with a smooth surface and well-sharpened edges.
The number of sharpening passes depends on the degree of wear of the blade. We must pay attention to excessive sharpening additions that can cause overheating and hardening of the material in the tooth cavity, respectively the appearance of martensite in the tooth cavity, which is the main cause of cracks.
During sharpening, due to the wear of the stone, it changes its shape and periodically needs to be corrected with the help of a dresser. This correction of the stone has the role not only of returning the stone to its original shape but also of refreshing the cuts of the abrasive granules.
On our website you can find information about grinding stones.
These are the technical parts related to sharpening, but as with any work process, you must take safety measures during sharpening as well. In order to ensure the protection of employees against the dangers to which they are exposed, they must be equipped with protective equipment.
The individual protective equipment includes the following:
- work overalls and protective shoes;
- hearing protection and protective glasses;
- gloves and a protective mask.
Before starting the work, the operator will check the state of the machine, the control devices (start-stop and change the direction of movement), the existence and state of the protection devices.
We have left behind the question that presents the greatest interest: How can we increase the durability of the cutting and implicitly the productivity?
In order to reduce the frequency of sharpening and to keep the teeth of the blade in an optimal shape for longer, we recommend the use of blades with stellite teeth, because they are more durable.
Band saw blades for cutting logs with stellate teeth are blades to which an alloy called stellite*, based on cobalt, is applied to the tip of the teeth, having increased wear resistance and at the same time allowing higher cutting speeds.
These bandsaw blades are chosen in the following cases:
- when the increase in the cutting time of the blade between two sharpenings is observed;
- when the quality (roughness) of the resulting timber surface is very important;
- when cutting hard wood essences;
- when it is aimed that the loss in sawdust is small;
- when cutting frozen wood.
But the most important element that increases the durability of the saw is the peeling of the log. It is known that the bark of trees contains hard particles starting from very fine sand to pebbles, mud that in the process of tree growth are included in the bark and directly affect the cutting both when the tooth enters the log and when it exits. To avoid these problems, it is necessary to peel the logs, which can be done manually or with special machines.
If this is still not possible, it is recommended to at least wash the log of deposits and use pre-cutters that remove the bark of the log before the saw blade.
Below is how a professional peeler works. Although the investment in such a device is significant, the benefits are also proportionate. It is possible to double or triple the cutting time of a blade between two sharpenings and significantly decrease the damage to the blades. In order to further minimize damage to the bandsaws, it is recommended to install a metal detector in the line, especially if the logs come from areas where battles were fought in the Second World War.
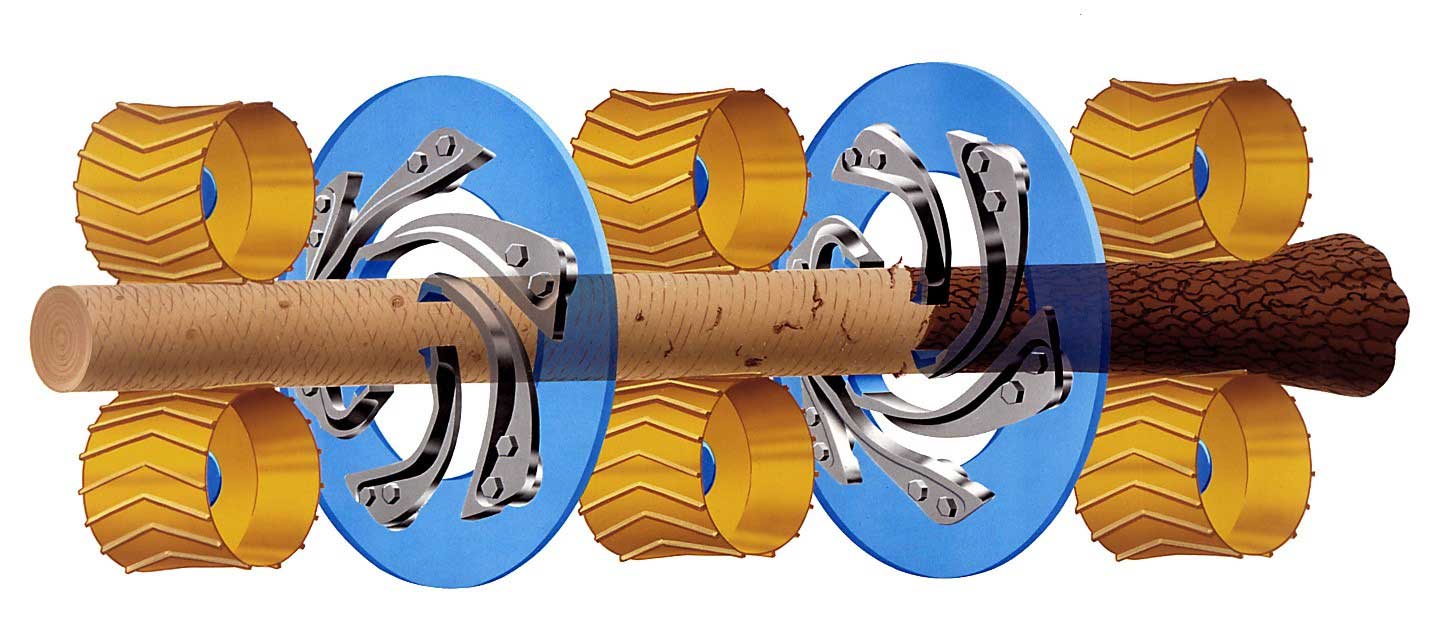
Did you know that?
A stellated bandsaw blade can be resharpened approximately 8 - 12 times, after which a new stellation is necessary. The number of resharpenings depends a lot on the cutting conditions: how clean the log is, the number of operating hours between two sharpenings, the essence of the cut wood, the performance of the sharpening machine, etc.
Did you like this article? Subscribe to the newsletter and you will receive the latest materials by e-mail once a month. You can also find us on Facebook!